
VISI PEPS Wire
VISI PEPS Wire - Reliable Wire EDM toolpaths and proven CNC Code
VISI PEPS-Wire incorporates the industry leading PEPS Wire EDM CAM system, developed specifically for the precision engineering, tool-making, mold & die, press and extrusion tool industries, within the VISI design environment. Fully feature based, VISI PEPS-Wire provides automatic feature recognition of wire features including tapered, variable taper and 4 axis directly from solid geometry. Features are easily machined creating reliable Wire EDM toolpaths and proven CNC code for all Wire EDM machine tools.
Features at a glance:
- Extensive CAD interfaces
- Comprehensive machine and postprocessor database
- Automatic feature recognition including 4 Axis, variable taper, variable land, taper & holes
- Roughing and finishing cuts easily applied to multiple punches or dies
- Multiple tagging options with auto tag removal
- Reverse cutting on roughing, finishing and tag removal passes
- No-core pocket destruction of round, irregular and tapered apertures
- Cutting technology change points can be applied to any cut
- Simple and intuitive tool to add multiple tags and corner relief
Extensive range of CAD interfaces and powerful modelling. VISI can work directly with Parasolid, IGES, CATIA, Creo, UG-NX, STEP, Solid Works, Solid Edge, Inventor, ACIS, DXF, DWG, JT Open, STL and VDA files. The extensive range of translators ensures that users can work with data from almost any supplier. Companies working with complex designs will benefit from the simplicity with which their customer’s CAD data can be manipulated. VISI can work directly with wireframe, solid, surface and mesh data or a combination of all four, providing the user with tools to work with any CAD model or to quickly construct the information from paper drawings ready for wire machining.
Intuitive operation user interface. The 2 and 4 axis machining operations give the user a choice of parameters such as machining direction, auto offsetting, lead on/off radius, tag distance, lead off distance, lead on/off technology to name just a few. Each parameter is accompanied by a bitmap giving the user additional information on how it will affect the resultant toolpath.
Automatic feature recognition.VISI PEPS-Wire offers powerful automatic feature recognition developed specifically for Wire EDM technologies. Detection of ‘through’ features including holes, open and closed pockets, constant taper (including constant radius and conic corner modes), variable taper, taper and land, variable land and 4 axis is effortlessly achieved at the click of a button. The resulting features are grouped appropriately so that they can be machined quickly and reliably using the preferred machining method and technology.
Feature modification tools. Using native VISI graphical tools it is very simple to edit advanced features such as 4 axis or variable tapers. User ‘constraints’ or ‘synchronization lines’ are easily added to 4 axis features and the results dynamically update; particularly useful when designing extrusion dies. Variable tapered features can be edited graphically by dragging the angle on individual faces of the feature; this is achieved using interactive graphical sliders found extensively throughout the VISI environment.
Multiple tagging and tag removal.VISI PEPS-Wire allows the user to provide multiple start holes on a part. The system can automatically establish tags near to the start of each new hole location. In VISI PEPS-Wire it is possible to select from several different methods of unattended machining. If your machine is equipped with automatic wire threading, then you will most likely want to run unattended as long and as often as possible. Unattended machining is performed by leaving the slugs attached while all of the preliminary cuts are taken. Numerous strategies are available to cut the part; for instance, taking all of the rough cuts before finishing, in which case all rough cuts are taken while leaving the tags attached, then the tags are removed, and finally the finish cuts are taken. Alternatively, take the rough and finish cuts while leaving the component or waste material in place and then remove the tag and finish this area.
Toolpath verification and simulation.The completed wire path can be simulated using rendered solid model graphics, including fixtures and target geometry. Any collisions that are detected are highlighted both on the model and via on-screen messages. As slugs become detached, the simulation advizes the operator and graphically removes the part, emulating the cutting process on the machine tool exactly. Toolpath verification also tests whether the completed part is removable from the component. It is also possible to perform a part comparison between target model and cut part, which highlights any rest material or gouges.
Post processor database. VISI PEPS-Wire supports a comprehensive range of EDM machines from leading Machine Tool manufacturers including Agie, Charmilles, Brother, Fanuc, Hitachi, Makino, Ona, Sodick, Seibu and Mitsubishi. Machine Tool supplied technology data is also included for supported machine tools together with JOB/Script file output for Agie and CMD file output for Charmilles. The advanced post processors are easily configured to suit different machine models and configurations.
Automatic Cutting Strategies. VISI PEPS-Wire offers predefined cutting strategies for automatic ordering of rough, finish and tag removal passes to accommodate common shop floor needs such as ‘attended day cutting’ and ‘unattended night cutting’. Other features include :
- 4 Axis ‘null span’ support including reliable offsetting where small spans are eliminated
- Square, conic and constant radius corner modes for variable taper
- Separate clearance for main cuts and tag removal available
- Additional M-Codes including ‘Stop/Optional stop’, ‘Power on/off’ and ‘Wire cut/Thread’ configurable at any point
- Automatic start hole creation using CAD points or user configurable start hole strategies
- Secondary wire selection for supported machines
- Incremental lead on points to help eliminate ‘witness marks’ on finished component
- Automatic approach and retract technology to allow power to be ‘ramped’ up and down gradually.
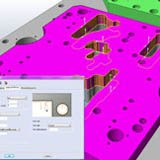
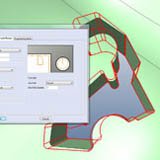
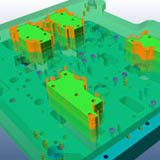
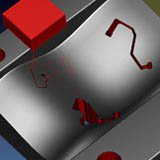