
VISI Machining 3D
VISI Machining 3D - Intelligent 3D Toolpaths with High Speed Milling routines
VISI Machining 3D creates intelligent toolpaths on the most complex 3D parts. Dedicated high speed milling techniques and built in smoothing algorithms create highly efficient NC code. Intelligent toolpaths will reduce cycle times on your machine, improve productivity and continuously produce high quality components.
Features at a glance:
- Extensive CAD interfaces
- Comprehensive tool library
- Adaptive roughing technology
- Operation rest roughing
- Combined finishing strategies
- Steep / shallow corner rest milling
- Full tool & holder gouge protection
- High speed optimized toolpath movements
- Full kinematic simulation
- Customisable postprocessors
- Reliable & efficient NC code
- Multi-threading processor support
Extensive range of CAD interfaces and powerful modelling. VISI can work directly with Parasolid, IGES, CATIA, Creo, UG-NX, STEP, Solid Works, Solid Edge, Inventor, ACIS, DXF, DWG, JT Open, STL and VDA files. The extensive range of translators ensures that users can work with data from almost any supplier. Companies working with complex designs will benefit from the simplicity with which their customer’s CAD data can be manipulated. VISI can work directly with wireframe, solid, surface and mesh data or a combination of all four, providing the user with tools to work with any CAD data or to quickly re-model parts ready for machining, fully utilizing the power of true hybrid surface and solid modelling.
Intuitive interface. A simple tree structure makes it easy to navigate around the machining operations. Machining parameters for depth of cut, step over, ramp angle etc. are input using a highly graphical interface. Most commonly used values, can be stored as default settings enabling the operator to use a company standard consistent method of machining. On line context sensitive help will guide the programmer through the available machining options.
Comprehensive Tool library with holders, cutting parameters and sister tooling. Catalogues of tools, holders, extensions, adapters, storing speeds, feeds, optimal cutting depth, stepover values and tool offsets along with tool and gauge lengths can be selected from user definable libraries. For longer machining cycles, VISI will keep track of the amount of machining completed. When the specified tool life has been reached the system will automatically call for a sister tool, minimizing the risk of damage to the part being machined, by worn or broken tooling.
Multiple roughing toolpaths.A combination of constant Z roughing, adaptive roughing, core roughing and rest roughing, combined with intelligent ramp, helical and planar entry methods provide the operator with the freedom to produce efficient NC code to suit any component. Combined with smooth corner radii and smooth transitions between passes, the tool will maintain the maximum feedrate on the machine tool, and prevent the cutter from dwelling in corners. For subsequent roughing operations, VISI will remember where remaining stock is left on the component and only machine in those areas. Wasted air cutting will be minimized and unnecessary rapid movements will be eliminated, while the cutter will avoid digging into areas where there is excess material, which could result in tool breakage. Where the starting billet is pre-machined, or possibly a casting, VISI will recognize and machine only where material exists, again eliminating wasted movement, and keep cycle times to a minimum.
Adaptive clearance. Adaptive clearance toolpaths allow the tool to rough the part in a unique way by roughing out from bottom to top. The principle behind this method is to machine large steps utilizing the full flute length of the tool with a small stepover and then machine the intermediate levels back up the part. Continually repeating the process until the entire component is fully machined. The tool remains on the part as much as possible and the toolpath automatically switches to a trochoidal type motion when the shape of the part requires. This toolpath ensures that there are never any full width cuts and guarantees a constant tool load. Tool wear is spread evenly across the cutting surfaces and the center of force is half-way up the tool, reducing deflection and the potential for vibration Using adaptive roughing, the cycle automatically adjusts the toolpath for efficient and safe machining, improving cutting conditions and allowing higher machining speeds to be maintained. The result is savings of up to 40% in actual cutting time.
ISO-Machining.ISO-Machining is based on single or multiple surfaces and machines the surface directly instead of creating a triangulated mesh. This strategy is ideal for machining groups of surfaces that make up radii as the contact point of the tool machines to the full edge of the geometry. This flexible strategy is also extremely useful for picking out small areas without having to machine the entire component. All toolpaths are fully gouge protected against neighbouring surfaces with multiple collision detection options available.
Flat surface machining of planar surfaces.For areas of the part which are flat, VISI will automatically detect these areas and machine them using a flat bottomed tool. The machining time for these areas will be significantly reduced and the surface finish will be greatly improved by using a flat tool.
3D step over finishing.The 3D stepover toolpath provides a constant surface finish irrespective of the component shape. By morphing the toolpath across the surface of the component, one toolpath will finish the entire job, keeping the tool on the surface, minimizing retract movements and eliminating duplicate cutter paths. As the toolpath step over is smoothly adapted to the shape of the part, shock loading of the tool will be minimized, enabling the machine tool to run at the optimum feedrate.
True spiral / radial finish machining. Both toolpaths make an ideal finishing strategy for circular components as they are based on an inner and outer circular limit. The spiral toolpath has only one start and one finish point guaranteeing the tool remains on the component eliminating any redundant moves or sharp direction changes. This toolpath will enable the machine tool to run at very high federates as it eliminates the acceleration and deceleration caused by sudden changes in direction. The radial toolpath allows upwards only, downwards only or zigzag machining parameters providing complete strategy control.
Parallel Plane finishing.Unidirectional and zigzag toolpaths can be set at any angle. Angle limits can be set for steep and shallow areas eliminating the need for complex geometry boundaries. Optimized cross-machining can be applied to steep areas within one toolpath. This automatically creates additional toolpaths at 90 degrees to the original toolpaths, machining the areas only where necessary to produce a constant surface finish across the entire component. Roughing mode within the Parallel plane toolpath can be used to rough and finish the part in one operation. Smooth stepovers and tangential extensions to the passes can be used to produce a better surface finish and smoother running of the NC file on the machine tool.
Constant Z / combined finishing. For components with steep walls, cutting in Z slices provides a good surface finish. VISI provides many options within the constant Z strategy to produce the best performance from this toolpath. Where the angle of the walls change, VISI can automatically adapt the slice heights of each level for shallow areas. Wireframe geometry can also be used to control the slice height and angle limitations can be used to eliminate passes in shallow areas. A helical option allows one continuous toolpath to be created which eliminates witness lines on the part and improves surface finish. Additionally a combined constant Z toolpath is available for finishing steep and shallow areas in one toolpath. This strategy allows steep areas to be machine using a constant Z method and shallow areas to be machined using a 3D constant stepover method. This strategy operates as a one stop finishing toolpath.
Leading curve machining and 3D curve machining.The operator can control the cutting area by machining between two driving curves across a model. Parallel machining will morph between the curve geometry using the curve shape as a toolpath guide. Perpendicular machining will run normal to the guide curves giving a choice of cutting directions, allowing more control of the machining method. 3D curve machining forces the cutter to run along the 3D curve in open space (without model geometry) making the strategy ideal for scribe lines and engraving onto the surface of the model.
Rest machining of fine details. Small features on a model will usually require rest machining with a smaller tool to completely finish the detail. The rest machining command will reliably detect areas left by previous tools, so that they can be re-machined. For very fine details, this process can be repeated as many times as required to make it possible to successfully machine with very small cutters. The toolpath can work from the outside to the center or from the center to the outside of small blends. For features, which are very close together, the toolpath will morph and blend together around obstacles to provide a smooth and flowing toolpath without any sudden direction changes minimizing the number of retract movements and helping to eliminate shock loading on the tool and keep feedrates as high as possible.
Short calculation times and batch processing. New algorithms provide very fast calculation times even for the most complex parts. High speed machine tools require huge amounts of data to keep them running efficiently. By keeping the calculation times as short as possible, unscheduled machine stoppages will be kept to a minimum. To maximize the deployment of the software, VISI uses multi threading technology to allow multiple operations to be calculated at the same time and batch processing to allow jobs to be queued for unattended calculation, out of normal working hours. To further speed up the preparation of programs, individual operations can be postprocessed separately, so that machining can start on roughing operations while finishing operations are still being calculated.
Tapered tools supported on all cycles. Where models have no draft, it is possible to use tapered tools to machine draft directly onto the model. Straight tooling will require modification of the model to add the correct draft angle before machining can start. Adding draft to imported geometry can often be a very difficult and time consuming task.
Graphical toolpath editing and reordering. Once the toolpath has been calculated, it is possible to easily trim sections of toolpath and edit the rapid movements to optimize the cutting method to suit individual components. The sequence of operations can also be easily changed; a simple drag & drop concept can be used to modify the operation order. Toolpath editing provides the operator with the freedom to quickly arrive at their preferred machining method and sequence of operations.
Smooth point distribution, and smooth transitions. VISI creates each toolpath with an even distribution of co-ordinates. By sending smooth and efficient CNC code to the machine tool control, it will reduce unnecessary acceleration and deceleration on the machine, making it possible for the machine to operate as close as possible to the programmed feedrate. All the toolpaths have smoothing radii in the corners, smooth transitions between passes and options for looping movements linking the ends of each pass. All these elements help the machine tool to run faster, prevent sudden direction changes and eliminate excessive strain on the tool.
Full gouge protection. All 3D toolpaths are gouge checked against neighbouring surfaces to eliminate the possibility of a tool collision. In addition small smoothing radii are automatically added to internal corners. These movements stop the tool from dwelling in the internal corners, which can cause the tool to pull into the job creating an unexpected gouge, which would not be detected by toolpath verification.
Tool holder collision checking. Checking the tool and the holder against the model provides a warning of a potential collision, together with relevant information about the tool length required to complete the job. By limiting the Z cutting envelope for the tool, it is possible to use several tools to machine a cavity, taking advantage of the rigidity of shorter tools to remove most of the material.
Template machining. To speed up the programming, templates containing tooling, operations, feeds, speeds, depth of cut etc. can all be stored for reuse on similar or families of parts. Applying them to a new part will automatically create a new set of toolpaths using the same settings, greatly reducing programming time and using company standard feeds, speeds, methods and tooling which have been proven on a previous job.
Configurable postprocessors and set-up sheets. An extensive library of postprocessors is available to suit most machine tools. In addition all postprocessors are fully configurable to suit individual requirements. Canned cycles for drilling and boring, subroutines and cutter compensation can be output along with 3+2, and full 5 axis CNC code for use on the shop floor. Bespoke post processors can also be written for complex one-off machine tools. Set-up sheets are automatically generated with information about the datum position, tooling, cycle times, cutting envelope etc. The contents and layout of the set up sheet can be tailored to match the needs of each user and output as either HTML or XLS format.
NC Feed optimization. NC code can have federate optimization applied to slow the feedrate when entering areas where larger amounts of stock occur, this all allows the machine tool to run faster and smoother. This option is constantly comparing the amount of material removed against the actual mechanical forces applied to the tool. The result of this sophisticated volume comparison tool provides a better toolpath, extending the cutting life of the tool while using the machine safely at the upper end of its performance regime.
High speed machining and hard metal machining. Many toolpaths inside VISI tailored towards high speed machining and hard-metal cutting. Smooth corners, smooth stopovers and arc fitting are used to minimize sudden direction changes. The elimination of tool retracts, maintaining a constant tool load and optimized NC code make it easy to successfully program high speed machine tools with VISI.
2D machining and Manufacturing Feature Recognition.Toolmaking applications often contain components which require 2D machining. Due to the integrated nature of VISI, manufacturing of individual plates can be completed using feature recognition. Drilled hole features and apertures are automatically selected with the correct drilling cycles and 2D milling routines applied creating practical CNC code for the most complex plates.
Kinematic simulation. Toolpath verification can be applied using the real machine dimensions and limits with the kinematic simulation. Cutting tool, holders, jigs and fixtures can all be checked when running the kinematic display. Any gouges on the toolpath against stock, tool or any other part of the machine tool will be graphically highlighted. A comprehensive list of tested 3, 4 and 5 axis machine are available. Hexagon engineers are also available to help with the construction of any bespoke machine.
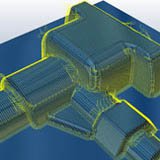
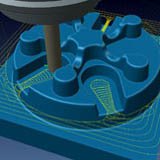
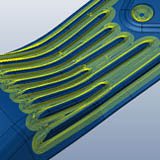
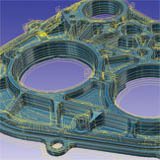
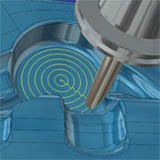