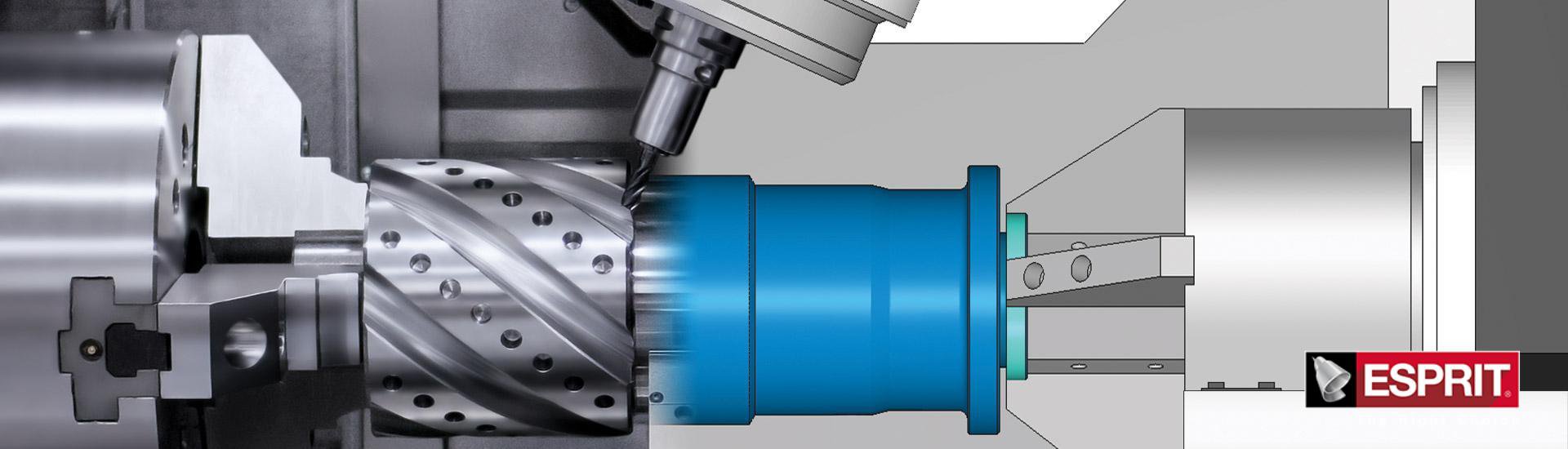
Multitasking
Powerful programming, optimization, and simulation for millturn and multichannel machines
ESPRIT provides a natural workflow with an extensive capacity for programming, optimization, and simulation of multifunction, multitasking, and multichannel millturn machines. Supporting any machine configuration and size, ESPRIT is the right choice for companies in a wide range of industries from aerospace and power generation to micromachining in the electronics and medical sectors. With a powerful suite of machining cycles combined with advanced process synchronization, program optimization, accurate on-screen machine simulation, and edit-free G-code, ESPRIT will utilize the full capacity of the machine tool.
- Any machine, any industry, any application, ESPRIT is the right choice!
- A powerful suite of machining cycles
- Advanced process synchronization and program optimization
- Accurate on-screen machine simulation
- Machine-optimized G-code
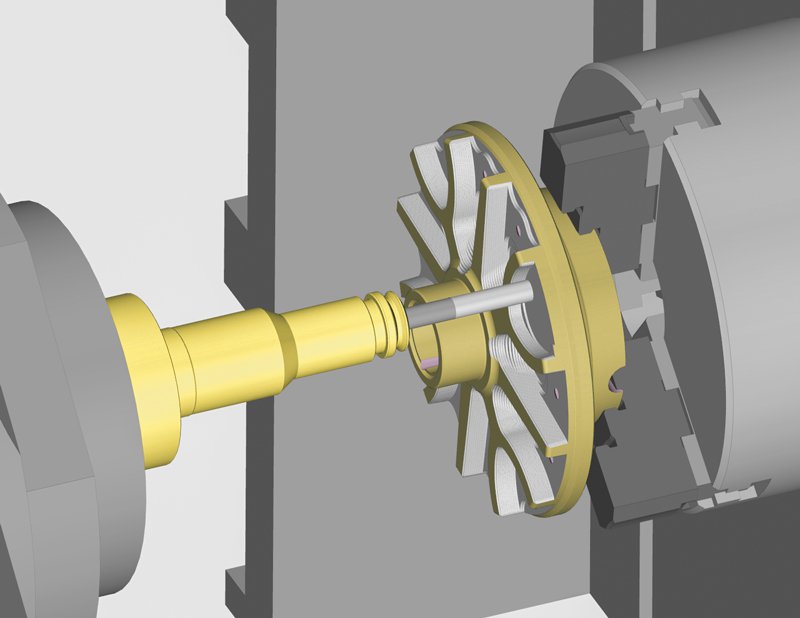
Machine-Aware Multitasking
ESPRIT uses a digital twin of the CNC machine for setup, programming, optimization, and simulation. This awareness and knowledge of the machine’s capabilities and limitations power ESPRIT’s most advanced features — from high-speed machining to post processing — simplifying the programming process while utilizing the full capability of the machine. With machine awareness, CAM programmers can make better choices and see improved machine performance.
- Using a digital twin for programming, optimization, and simulation
- Provides awareness and knowledge of the CNC machine
- Empowering programmers to fully exploit the machine's capacity
- Significantly improving the machine’s performance on the shop floor
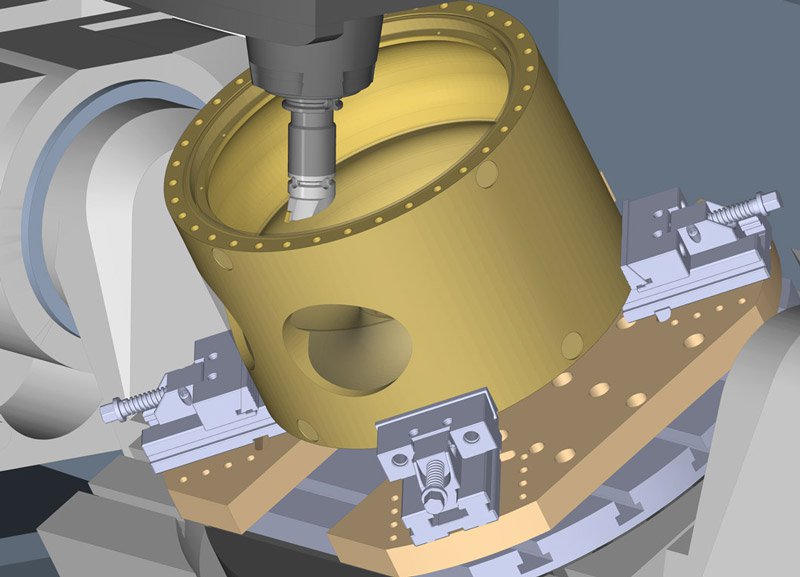
Milling on a Lathe, Turning on a Mill
With ESPRIT’s Modeless Programming™, combine traditional milling and turning cycles, freeform 3-axis and 5-axis machining, on-machine probing, and part handling cycles in any order, utilizing any table, head, turret, or spindle available on the machine.
The process plan for a part is maintained separately from the program as run on the machine, so ESPRIT will automatically adapt the process plan to the new situation reflecting any changes to the setup or machine. With machine swap, there is no reprogramming when moving from prototype to production or from machine A to machine B due to shop scheduling.
- Any milling or turning cycle, in any order
- Automatic updates reflecting changes to the setup or machine
- Easily move from prototype to production, or machine A to machine B
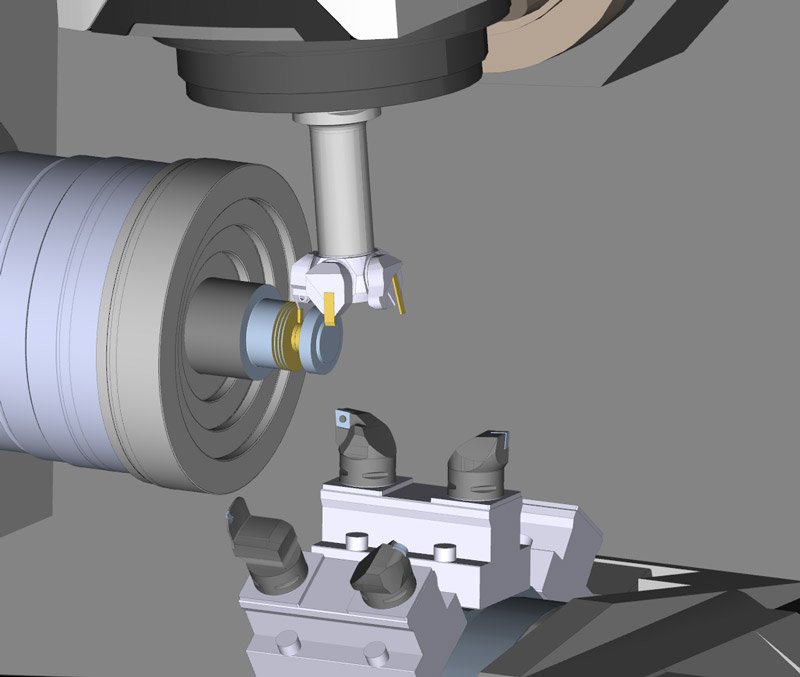
Synchronized Machining
ESPRIT automatically synchronizes machining cycles as you create them, with manual
synchronization available for advanced program optimization. As a result, cycle times on the
machine are minimized and the full capacity of the machine is utilized. Use sequential mode to
optimize cycle times and synchronize the machining cycles for short runs of a single workpiece.
Accomplish maximum throughput in parallel mode, where two parts are cut concurrently using the
main and sub-spindles. When cutting with two or more tools simultaneously on the same
workpiece a master channel is chosen for control of the shared spindle or rotary axes. The result is
a complete, optimized program that synchronizes the machining cycles with workpiece handling
and setup changes, including bar feed, reposition, cut off, eject, transfer, and re-chucking.
- Automatic synchronization of machining cycles and workpiece handling
- Simultaneously machining one, two, or more workpieces
- Resulting in minimized cycle times and full machine utilization
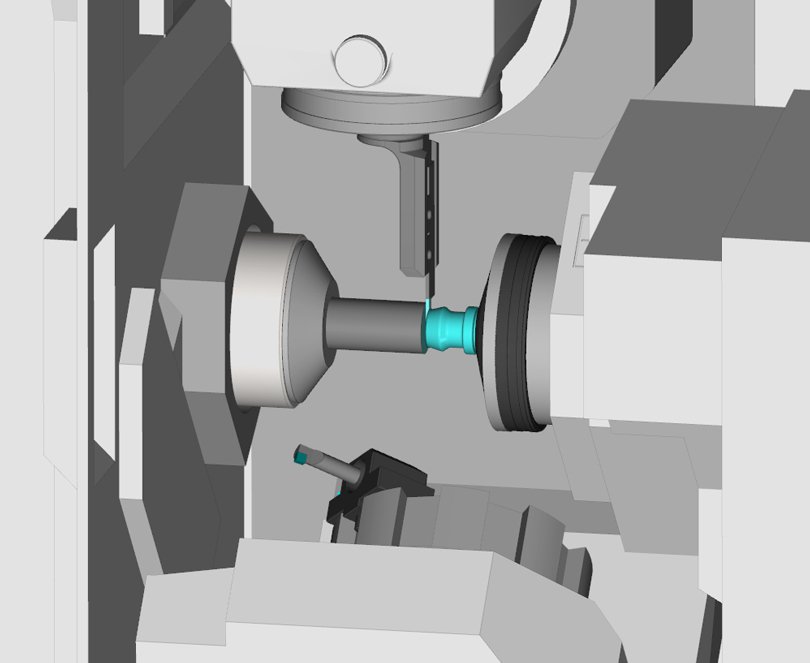
Automatic Link Generator
With a great deal of simultaneous action taking place inside a multitasking machine, collisions can
be a constant risk. ESPRIT’s link generator automatically creates machine-optimized, collision-free
positioning and rapid moves, saving significant time during programming and on-machine prove
out. The link generator is indispensable in making sure that all rapid positioning is performed in a
safe and efficient manner that considers all the tooling, workpiece, and machine components.
- Automatically creates machine-optimized, collision-free positioning and rapid moves
- Considers all the tooling, workpieces, and machine components
- Saves significant time during programming and on-machine prove out
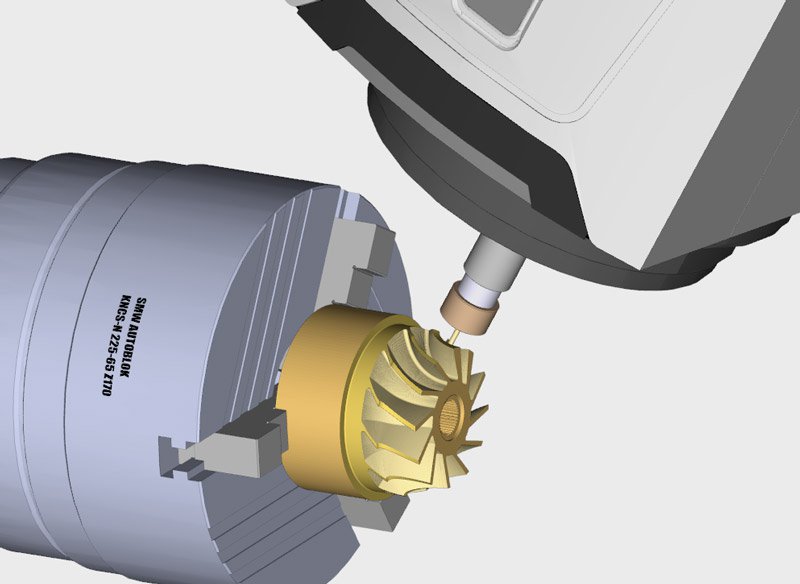
Adaptive Machining
Adaptive machining cycles provide great flexibility to utilize the full capability of the CNC machine.
With a single user interface, program any cutting cycle using any combination of channel, turret,
and spindle. Use ESPRIT’s high-speed machining cycles, ProfitMilling and ProfitTurning, for
shorter cycle times, improved surface quality, and longer tool life. Take advantage of rotary
machining cycles to overcome limited X-axis stroke, advanced turning cycles with multi-function
tools, and extensive drilling options with part and/or tool spinning on- and off-center. ESPRIT
automatically updates your programs in real time as you make changes to tooling, turret and/or
channels.
- Using any combination of channel, turret and spindle
- High-speed machining for shorter cycle times, improved surface quality, longer tool life
- Rotary machining to overcome limited X-axis stroke
- Updates in real time as changes are made to tooling, turret, or channels

Full Machine Simulation & Verification
All the multitasking action of the machine is displayed in real time. This provides an incredibly accurate, animated view of the entire machining process, including the synchronized motions of all the machine’s components: cutting tools, turrets, spindles, heads, steady rest, and tailstock. Start a simulation at any point in the program using ESPRIT’s knowledge of the current state of the workpiece and each channel of the machine. Analysis is available to review the details of each cutting cycle while the analytics provide reports for:
- Potential part violation and collisions
- Axes limit monitoring and overtravel detection
- Axes acceleration exceptions
- Channel conflicts in the event of incompatible instructions
Ask for Pricing
Used in thousands of shops all over the world, ESPRIT CAM software is a global favorite for all types of machining applications.
Ranging from small hometown job shops to multinational enterprises.