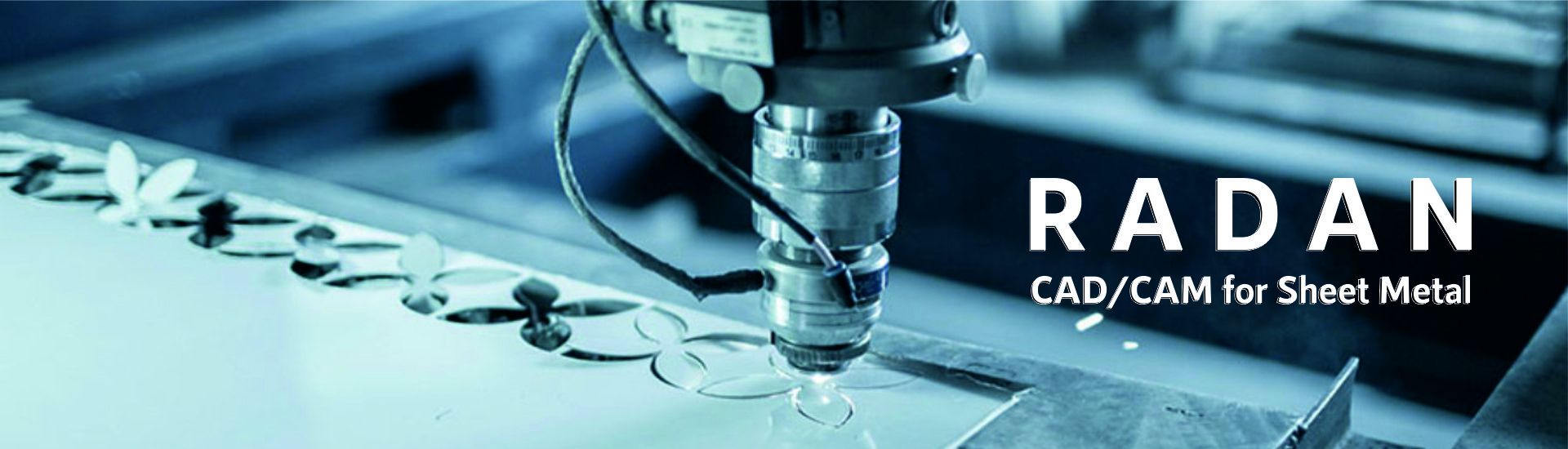
RADAN Designer
Modelling for Manufacture
RADAN | Designer is the ideal CAD solution for CAM. From electrode design to model repair to reverse engineering, RADAN | Designer is the ultimate manufacturing CAD solution for taking complex models to manufacture.
Features at a glance
- Easy to learn, intuitive user interface
- Direct modelling CAD environment
- Combined surface, solid & mesh modelling environment
- Seamless links to our CAM platforms
- Sketching with automated region creation
- Impressive surface repair of third-party CAD models
- Extensive list of CAD import formats
- Dedicated reverse engineering suite (as of 2021.0)
- Powerful 2D-Drawing environment
- Targeted functionality for the sheet metal industry
UNFOLD PREPARATION
Several powerful sheet metal functions are available to prepare a part for unfolding. RADAN | Designer has functionality to correct the thickness, change bend radii and make changes to flange angles and lengths.
UNFOLDING
Unfolding a sheet metal part couldn’t be easier. RADAN | Designer offers a flexible material library and several calculation methods to create the correct unfolded shape. Available are unfolding using a setback at 90 degrees, a k-factor, DIN correction, or using only the V-width of the die that will be used to bend the part.
Unfolding parameters, such as bend allowances, can be controlled independently of the geometry, enabling an accurate development that is based on the actual bending machines and tooling to be used in production.
This leads to:
- More accurate flat blanks
- More accurate folding; and
- Ultimately a higher quality product
EXTENSIVE RANGE OF CAD INTERFACES
RADAN | Designer imports data from a wide variety of exchange formats including Parasolid, IGES, STEP, ACIS, DXF, DWG, STL and VDA files as well as native data from the following CAD systems:
- Catia V4 & V5
- Pro/ENGINEER & PTC Creo
- Autodesk Inventor
- Siemens NX
- SolidWorks
- Solid Edge
WORKING WITH 2D DATA
RADAN | Designer supports the import of DXF and DWG files allowing the user to transform existing 2D data into a 3D model by simply reusing the imported profiles from the original data. Imported data automatically creates sketch profile regions making the transformation from 2D to 3D easier than ever.
DIRECT MODELLING
Direct modelling frees the user from the constraints of a traditional modelling system. Rather than modifying a lengthy series of parameters to make a design change, direct modelling allows the user to push, pull and drag the geometry to obtain their desired shape. These changes can be completely freeform or driven by numeric increments and measurements taken from existing geometry.
Knowledge of how the original model was constructed is no longer necessary and design changes are not constrained to the original methods of creation. Direct modelling gives the user complete freedom of construction whether creating a new component or modifying an existing design created in any of the myriad of CAD formats that EDGECAM | RADAN | Designer supports.
The extensive range of translators ensures that users can work with data from almost any supplier. Very large files can be handled with ease and companies working with complex designs will benefit from the simplicity with which their customer’s CAD data can be manipulated.
MODEL MODIFICATION
The sheet metal part can be modified by adding bends, opening closed edges, splitting faces and creating corner clearances using powerful and intuitive workflows.