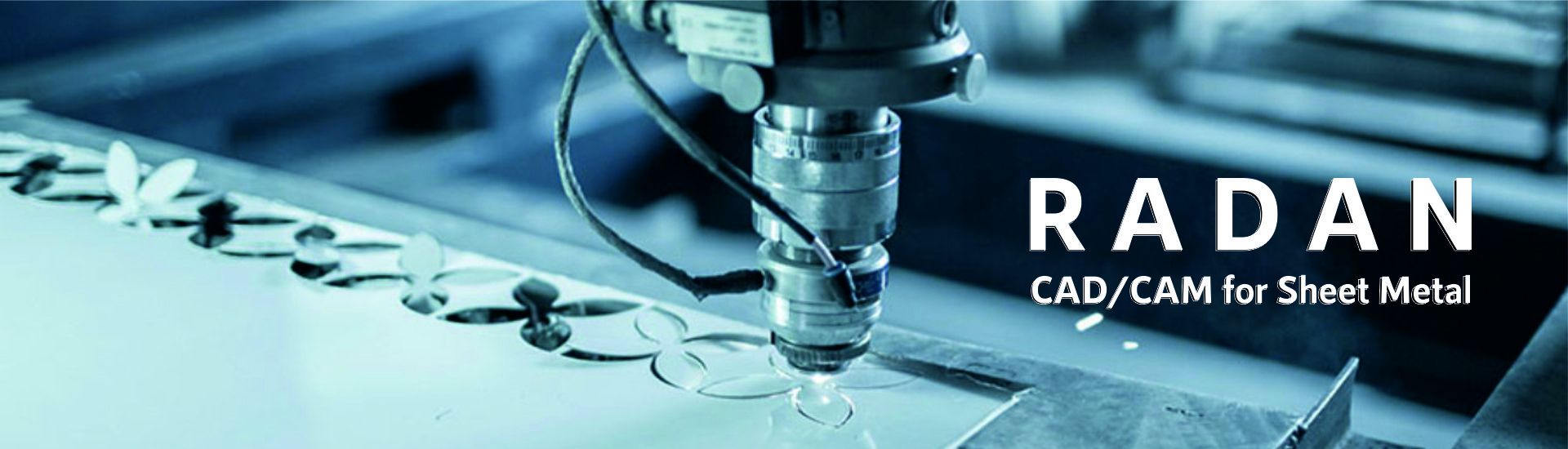
RADAN Radcombi
CNC programming for all your punch, profile and combination machines
Radcombi is a machine independent product developed to drive punch, profile and machines which incorporate both technologies. It provides your operators with the tools they require to reduce lead times and optimize your machinery efficiently and safely. RADAN’s punch/profile solution delivers optimization for punch, profile and combination machine tools.
Features at a glance
- Drag and drop data input
- Batch processing of DXF/DWG including healing
- Automatic tooling/sequencing
- Automatic part removal
- Graphical program verification
- Single part true shaped nesting
- Project nesting incorporating user definable reports
- Automatic common line cutting
- Automatic remnants, sheet scrapping and off-cuts
- Quick estimates for parts or nests
- Simple intuitive interface with clear and simple icons
- Supporting machines' advanced features
- Improved machine/tooling efficiency
- Reduced lead times and increased productions
Efficiency is everything
Radcombi is a fast, modern programming application designed and written by RADAN to assist a programmer in transferring data from CAD to NC code. The seamless interface, the automatic processes all assist the operator in this process. Unfortunately in reality production workflow is not always that consistent. Problems downstream, manufacturing change requests, reject rework requests all require an operator to be as fast and efficient. Radcombi enables an operator to jump into the programming process at the point where that the change is required; but it does not necessarily demand that the whole programming process is repeated.
A machine tool is only as efficient as the software driving it, so that is why we personally install every Radcombi post processor to ensure that it is commissioned to match your machine tool and controller. It is your production efficiency that it is going to be controlling, that’s why your software is important to us.
Seamless programming
Radcombi seamlessly integrates the whole programming process of geometry creation, tooling, nesting, sequencing, code generation and finally DNC connectivity to the machine controller. The seamless integration delivered by Radcombi provides an easy to use experience for your operators, whilst accuracy and consistency of programming is maintained with the collation of process critical data in the Manufacturing Database (MDB).
Material, tooling and machine tool specific data are stored in the MDB in readiness for instantaneous distribution when required to assist an operator or automated process. Understanding the sophistication and the limits of each machine tool individually is the key to driving it efficiently; Radcombi will assist your operators to optimize your manufacturing capacity to within those limits for all of your machines from a single system.
Tooling optimization
Optimizing the tooling used by a punch machine is paramount to the efficient programming of a punch machine and thus the reduction of the cost to manufacture a part. Simply optimizing conventional tools on a part and their location in the turret or tool rail is no longer sufficient, as tooling suppliers are providing more sophisticated tooling such as close to clamp slitters, wheel tooling, de-burring tools, scribes and flexible part marking tools. Radcombi understands the constraints of tools and the necessary NC codes required to support them.
Radcombi’s orientation specific tooling permits multiple tooling setups to be applied to a part for different nesting orientations and different machine tools. This enables the downstream nesting process to fully optimize material utilization by part rotation, which may have otherwize been restricted due to tool rotation limitations. The same functionality also optimizes preparation of parts for removal processes on more sophisticated machine tools. Whilst a part may be capable of dropping down a chute or being picked at one orientation, at another orientation it may not be suitable. Orientation specific tooling enables the appropriate part removal processes to be applied to complement the part orientation during nesting.
To minimize programming lead time identification and manipulation of tooling is paramount to an operator, Radcombi provides this capability with the user customisable interactive tool list. The easy to use interface enables an operator to quickly identify and interact with tooling at process critical stages.
Radcombi supports automatic common line cutting when profiling. This enables the downstream nesting process to fully optimize material utilization, whilst also benefiting from reduced cutting times and assist gas costs. Parts identified for common cutting can be controlled to cut in clusters to maintain sheet rigidity and remove tolerance problems associated with common cutting in large quantities
Power and control
The power of automation with the ability to control by your preferences. The Radcombi programming solution provides your operators with easy to use software that can be educated to adopt your preferred practices and processes. Tool selection, tagging, preferred removal procedures, preferred punching sequences all these and more can be defined relative to material type, thickness and machine tool in the Manufacturing Database (MDB) The introduction of new customers, new products or new machines brings into your manufacturing environment the need to control new material, tooling and new practices. The MDB ensures consistency of programming for these new criteria for all of your machines, which translates to less rejects, less rework and higher returns.
The fully integrated Project Nester provides your operator with an instantaneous overview of your punching demand. Automatic rectangular nesting, single part true shape nesting and manual drag and drop nesting techniques enable your operator to quickly, easily and efficiently meet your ever changing production and customer demands. If material utilization is critical to your business upgrading the nester to Radnest our true shape nester will raize your material utilization whilst also providing further advanced nesting tools for your operator.
Understanding the sophistication and the limits of each machine tool individually is the key to driving it efficiently; Radcombi will assist your operators to optimize your manufacturing capacity to within those limits for all of your machines.